IO-Link Safety with Bihl+Wiedemann – simple, fieldbus-independent, perfectly integrated
With IO-Link Safety, safe and standard signals can be seamlessly exchanged with intelligent sensors – in a compact, cost-effective, and reliable way.
IO-Link Safety is particularly smart when combined with ASi-5 Safety. AS-Interface offers a simple, cost-effective, and resource-saving wiring solution as an alternative to Ethernet-based round cable solutions – without plugs, sockets, and pre-assembled cables. The advantages of IO-Link Safety are fully retained, complemented by the strengths of AS-Interface.
All data that IO-Link Safety can provide, such as safe and standard data, as well as additional information, diagnostics and parameters, are mapped to ASi-5 Safety. This makes ASi-5 Safety the optimal shuttle for IO-Link Safety devices, but often also directly the ideal solution. Especially where there is no suitable IO-Link Safety device, an ASi Safety Module or device is ideal, for example for applications with classic safety switches with OSSD output or floating contacts such as light curtains or emergency stops, but also for controlling an STO of a drive. Discover our ASi-5 Safety Input Modules and our new fully configurable ASi-5 Safety Module with up to 14 safe inputs and two safe outputs, which is suitable for almost all applications.
What is IO-Link Safety?
IO-Link Safety is an extension of the IO-Link standard that was developed specifically for safety-related applications in industrial automation. It enables the secure transmission of data between safety-relevant devices, such as light curtains or safety sensors, and the IO-Link master. These, in turn, are typically connected to the automation system via a safe fieldbus. Thanks to the standardized M12 connection and a range of up to 20 meters, IO-Link Safety offers a well-thought-out point-to-point protocol, including parameter backup. In doing so, it meets international safety requirements such as PLe (Performance Level e) and SIL3 (Safety Integrity Level 3).
The most important advantages of IO-Link Safety:
Safety-related and non-safety-related signals are transmitted over the same standard interface
Full data transparency enables comprehensive diagnostics for predictive maintenance and rapid troubleshooting
Individual parameterization of the nodes via the same connection
Easy device replacement because all parameters are stored as a backup in the IO-Link Safety master
Integration independent of system and manufacturer
IO-Link modules from Bihl+Wiedemann feature interfaces for almost all standardized fieldbus systems found in industrial automation technology, no matter which control system is used. System- and manufacturer-independent use is made possible by the ASi-5 technology, which also enables significantly faster transmission of larger data volumes. This means that many applications can be implemented easily and cost-effectively.
Save valuable resources
The flexible configurability of the IO-Link module offers many advantages. Using AS-Interface also means you need less costly connectors and cables, thereby significantly reducing installation times and material costs. This way, you can save valuable resources such as copper and plastic, which are needed for manufacturing. Even the energy consumed during cable production is significantly reduced. And last but not least, there is a positive environmental effect when it comes to disposal – less waste is generated.
Advantages of IO-Link Safety with Bihl+Wiedemann
You benefit in many ways when integrating IO-Link Safety devices via AS-Interface solutions from Bihl+Wiedemann. Learn more about the general advantages of ASi.

Smart
wiring concept
The amount of effort required for wiring is reduced because all nodes – IO-Link Safety devices, IO-Link devices, standard sensors, and safety modules – are connected to an unshielded 2-core cable using piercing technology. Because no connectors are required, you also save costs and valuable resources. Furthermore, the maximum IO-Link or IO-Link Safety cable length of 20 m is almost irrelevant because the IO-Link Safety masters can be distributed as desired along the ASi cable, which can be up to 200 m long.
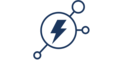
Smart
energy distribution
In round cable solutions, the respective connector indirectly determines the “limit” for individual IO-Link masters and for the total current of all IO-Link Safety masters connected in series. With ASi, no loop-through from module to module is needed. The AUX supply is done over reverse polarity protected profile cables, so each IO-Link Safety master draws its energy individually – at 20 A per AUX cable.
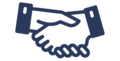
Close cooperation
with device manufacturers
Bihl+Wiedemann works very closely with leading IO-Link Safety device manufacturers. This allows us to ensure that the interaction between the PC software, IO-Link Safety master, and the respective device is as smooth and convenient as possible for the user.

Extremely simple
commissioning
Our convenient configuration tool makes it easy to integrate IO-Link Safety masters and to parameterize the connected devices very comfortably. You can simply select the IO-Link Safety device from the software, and you will be supported graphically when parameterizing the IO-Link Safety devices. Live device parameterization gives you direct control over the settings while being online.

Automatic parameterization when replacing devices
Our PC software makes it easy to copy and reuse parameters from IO-Link Safety devices. This applies both within projects and across various projects. The copy function saves a lot of time and reduces parameterization errors, especially when using many IO-Link devices.
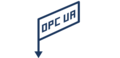
Integrated
IT interfaces
All our ASi-5/ASi-3 Gateways have an OPC UA server and a REST API as IT interfaces. This enables seamless integration into IT systems, such as cloud-based databases. Process, parameter, and diagnostic data from the IO-Link Safety devices can therefore be transferred easily and cost-effectively to the cloud or HMI – a prerequisite for modern systems in the age of Industry 4.0.

Reduced IP
management complexity
All safety-related and non-safety-related signals – and in a gateway with two ASi circuits, this data comes from well over 100 ASi modules – are transmitted to the PLC in a compact and bundled form. This means that you only have to assign and manage a single IP address, which, in many cases, significantly reduces the effort required for cybersecurity.
IO-Link Safety with Bihl+Wiedemann
IO-Link Safety is an extension of IO-Link with an additional safety communication layer on the master and device side. These then become the IO-Link Safety Master and IO-Link Safety Device. We are currently developing our own IO-Link Safety Master in collaboration with leading IO-Link device manufacturers. IO-Link is already perfectly suited for use with safety-related components from Bihl+Wiedemann.
The IO-Link Safety master is integrated as an ASi-5 node into the ASi network
IO-Link Safety devices can be integrated into the ASi network along with IO-Link devices, standard sensors, standard actuators, and safety components
All process data of the IO-Link Safety devices is available via cyclic ASi communication
All IO-Link parameters can be conveniently adjusted through the Bihl+Wiedemann Software Suite or acyclically via the control system
Diagnostic information from IO-Link Safety available via ASi
Thanks to close cooperation, our IO-Link Safety masters are optimally matched to most IO-Link Safety devices from leading manufacturers
If an IO-Link Safety device needs to be replaced, its parameters are stored in the IO-Link Safety master and are transferred automatically to the new one
ASi-5 Safety – the resource-saving partner of IO-Link Safety
For applications for which there is not (yet) a suitable IO-Link Safety device, or where IO-Link Safety devices do not provide any additional benefit (e.g. a simple EMERGENCY STOP), ASi Safety still almost always offers the perfect solution. The main difference between ASi-5 Safety and IO-Link Safety is the simple wiring system of AS-Interface. Would you like to learn more about the advantages of ASi-5 Safety technology? Then discover our ASi-5 Safety Input Modules and our new fully configurable ASi-5 Safety Module (BWU4277) with up to 14 safe inputs and two safe outputs, which is suitable for almost all applications.