- AS-Interface
Grinding machines from Schütte with AS-Interface: One system, two controllers, flexibility as desired
Alfred H. Schütte GmbH & Co. KG is a German machine tool manufacturer based in Cologne. The product range includes multi-spindle automatic lathes and 5-axis CNC grinding machines. The subsidiary Schütte Schleiftechnik GmbH, founded in 2007, develops and produces high-precision grinding machines and grinding solutions for the metalworking industry and is one of the leading experts in grinding technology.
The product portfolio includes a wide range of machines for various applications such as tool and mold making, medical technology, the automotive industry, and aviation. Schütte’s grinding machines are characterized by maximum precision, reliability, and efficiency and are valued worldwide for their quality and performance. Thanks to its many years of experience in the field of CNC grinding technology as well as investments in research and development and the resulting innovations, Schütte can achieve innovative solutions for its customers that are tailored to their specific requirements.
Schütte grinding machines
Schütte Schleiftechnik GmbH currently offers grinding machines from the 105linear, 330linear and 335linear series. While the 105linear, as a compact production machine, is designed more for manufacturing complex tools, such as drills or milling cutters, in large quantities and with high accuracy requirements, the 330 series, in particular the 335linear, are universal grinding machines with five axes, with which all requirements for the production and regrinding of tools of any kind can be realized. They can also be used to produce medical products, such as knee or hip implants.
Both series are available with a wide range of automation options for continuous adaptation and expansion – for example, in tool and workpiece handling for unmanned operation. This allows users to react flexibly to changing production requirements over the entire service life of the machine. Schütte enables the use of two different control systems for its grinding machines: SIEMENS SINUMERIK ONE and NUM Flexium+. While SINUMERIK ONE uses PROFIsafe via PROFINET for communication and is used together with the SIGSpro (Schütte Integrated Grinding Software) operating and programming interface, NUM Flexium+ relies on EtherCAT and works with NUMROTO.
Simple and compact – Schütte chooses AS-Interface
The history of AS-Interface at Schütte goes back to 1998, when ASi components were first used as part of the development of the 300 series – ASi valve terminals and limit switches for pneumatic valves. As Christoph W. Langen, Head of Electrical Design for Machine Tools at Schütte and significantly involved in the introduction, notes, the main reasons for the introduction of AS-Interface at that time were “firstly the simplicity of the technology itself and secondly the compactness of the ASi components, which is still not found in any other fieldbus solution today”. Schütte’s grinding machines – then as now – are characterized by a large number of movements in the machines. These are not hydraulic movements, but pneumatic ones. All these movements are controlled via ASi valves, which, together with the connections for the corresponding sensors, are located on extremely compact valve terminals with a very small installation footprint.
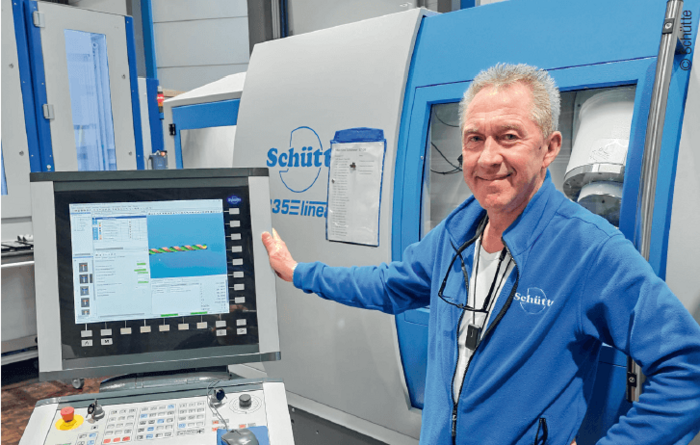
ASi also for safety
Over the 25 years since the introduction of AS-Interface, the complexity of the grinding machines at Schütte has steadily increased. This has become particularly clear when it comes to safety technology, which was still wired into the control cabinet in terms of hardware. Due to the positive experience with ASi in the standard area, Schütte therefore decided in 2013 to also implement all safety functions such as door interlocks with guard locking, contactless safety technology, or E-STOP circuits via ASi Safety at Work from this point onwards. “What convinced us at the time, in addition to the service and excellent support from Bihl+Wiedemann,” reveals C. Langen, “was the technology of the company’s safety gateways in conjunction with the ASi safety monitor. Simple handling, the most advanced technology. It was a big change for us at first, but in the end we realized that it couldn’t be easier than with ASi Safety.”
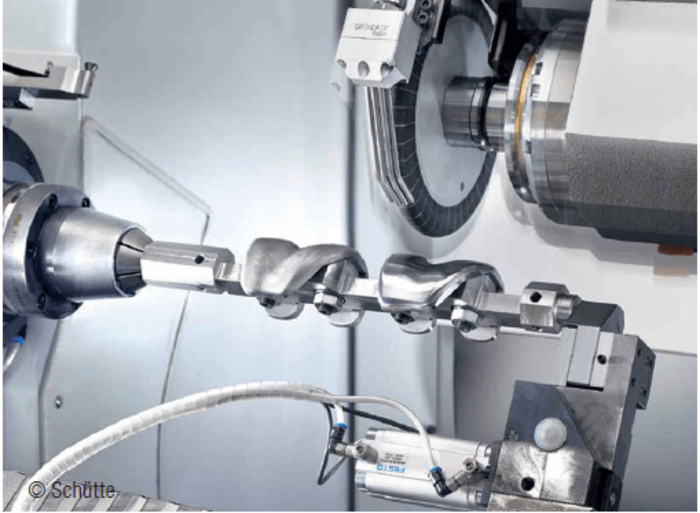
Schütte profits from many ASi advantages
The decision to use ASi and ASi Safety and the fact that a common infrastructure – the yellow ASi profile cable – can be used for safety and standard applications has many advantages for Schütte. One point that quickly convinced Schütte was the simple connection concept of AS-Interface. With ASi, modules can simply be “screwed on” to the yellow profile cable in the machine exactly where they are needed without connectors and pre-assembled cables using piercing technology.
According to C. Langen, this simplicity and flexibility are important because the mounting locations on the grinding machines can vary greatly, depending on the tool or workpiece handling and other optional equipment variants or extensions. It is therefore not surprising that Schütte’s grinding machines – starting with the connection of valve terminals with integrated inputs and end position sensors, flow monitors, and pressure switches through to door interlocks, door switches, and E-STOP buttons – are now equipped with the complete decentralized periphery via ASi and ASi Safety.
The Cologne-based company relies on the Bihl+Wiedemann portfolio for the selection of components, including ASi gateways and I/O modules. In addition to the ASi Safety Gateways, the company mainly uses ASi digital modules in IP67 for collecting the ASi signals in the machine as well as the Active Distributor ASi (BWU3374) and ASi Safety (BWU3248 and BWU3373), which can be used to easily integrate standard and safety components not having their own ASi interfaces into the AS-Interface network.
The complete connection of the decentralized periphery via AS-Interface provides Schütte with a further advantage. The grinding machines can be built much more efficiently, regardless of the control technology used, because the respective control concept only needs to be implemented in the control cabinet. Schütte builds its machine tools in cycles – in series of 12 machines. The configuration of the respective machine body is determined solely by its future functionality. Which control system is used in the end is irrelevant for the assembly at this point. The connection to one of the two variants of the machine control system is only established in the control cabinet by selecting an appropriate ASi Safety Gateway, which Bihl+Wiedemann offers with interfaces to many different (safe) fieldbuses.
In the case of Schütte, ASi-5/ASi-3 PROFIsafe via PROFINET Gateways (BWU3862) are used for machines with SIEMENS SINUMERIK ONE and ASi-5/ASi-3 Safety over EtherCAT Gateways (BWU3583) for machines with NUM Flexium+, which connect the ASi peripherals to the machine control system.
“Only the yellow ASi cable leads out of the machine body into the control cabinet,” explains C. Langen,”and simply by using an appropriate control cabinet, we can turn the machine into a machine with a NUM or Siemens controller.” And when all is said and done, a solution with AS-Interface is not only unbeatable for Schütte in terms of technology, but also for cost and efficiency reasons.
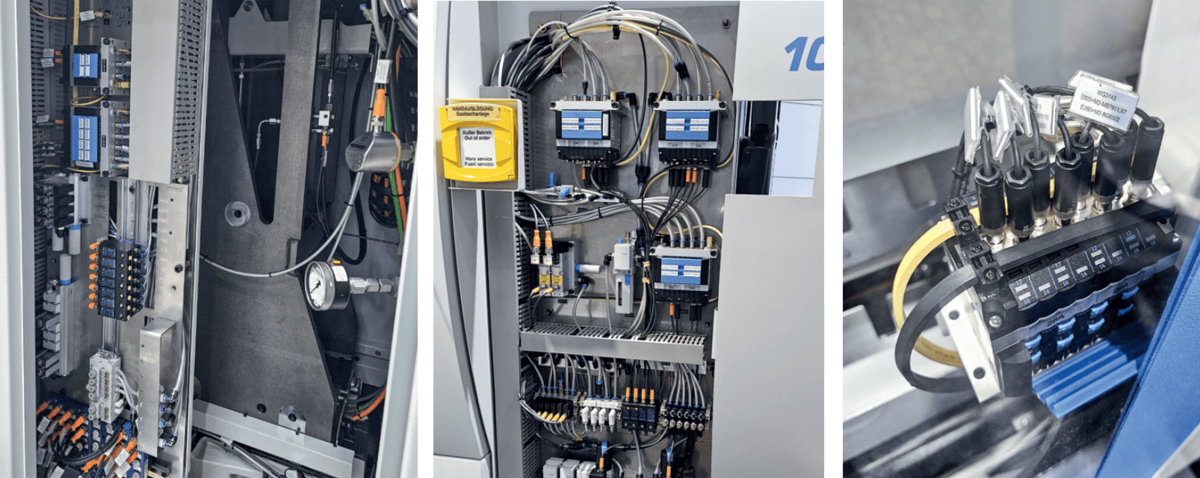
According to C. Langen, the company regularly reviews whether switching to a fieldbus system could make sense. However, it has been clear for many years that the use of PROFINET or EtherCAT components in the periphery would not only be significantly more expensive but would also make production much more complicated, as it would no longer be possible to produce the machine bodies independently of the control system, as described above.
ASi-5 and IO-Link
Schütte is constantly developing its grinding machines – also with a view to the future. In order to make the machines even more efficient and precise and to expand their range of functions, the company will not only rely on a new generation of control units and a new generation of control panels in the future but is also taking a major step towards Industry 4.0 by integrating IO-Link. A large amount of process data is recorded at various points in the machine via IO-Link sensors and made available for advanced diagnostics and predictive maintenance. At Schütte, for example, it is important that the machines are in thermal equilibrium. A constant temperature level must be maintained in the cooling lubricant systems, which are very complex and energy intensive. Possible defects or incorrect settings of a cooler, for example, which were previously undetectable, can be detected, diagnosed and rectified with the help of IO-Link temperature sensors. Fill levels, flows (of cooling lubricants), and pressures (e.g. in air handling) are also detected.
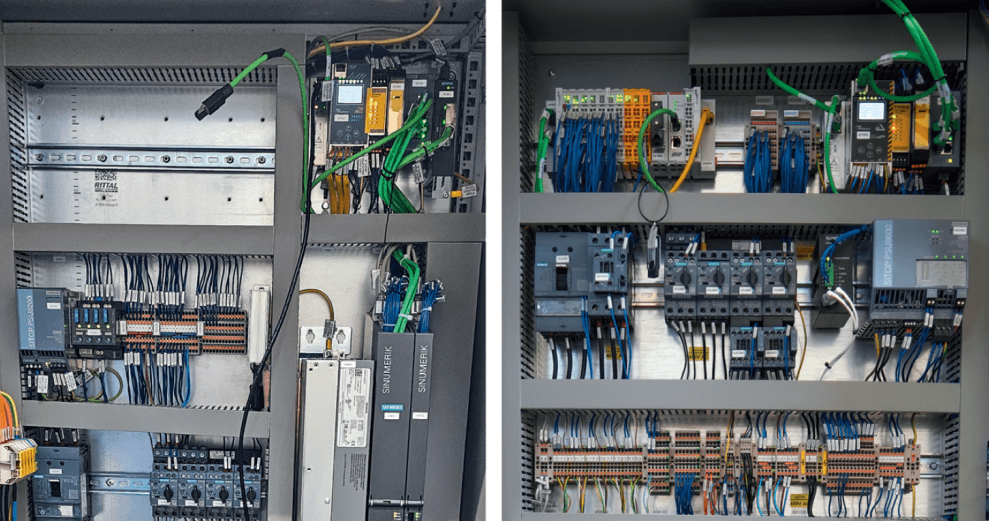
Against this background, it once again becomes clear how advantageous the decision was to connect the entire decentralized periphery in the machine via AS-Interface. This is because hardly any changes need to be made to the existing machine concept for the integration of IO-Link sensors. All that needs to be done is to replace the previous ASi Safety Gateway with an ASi-5/ASi-3 PROFIsafe via PROFINET Gateway or an ASi-5/ASi-3 Safety over EtherCAT Gateway. IO-Link devices can then be easily integrated into the existing ASi network via ASi-5 Modules from Bihl+Wiedemann with four or eight IO-Link master ports (BWU3819 or BWU4386) wherever they are to be used.
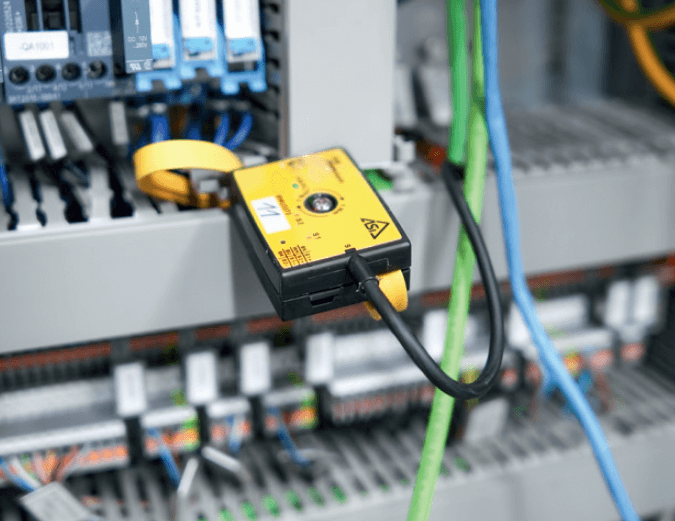
Compact, simple, high-quality, flexible in use, economical, and future-proof – attributes that aptly describe both the grinding machines from Schütte and the AS-Interface solutions from Bihl+Wiedemann. It is therefore no great surprise that the collaboration between the two companies has become a success story over the years – and one to be continued.